FlowScience Vs. the Competition - Scale Reduction at Methane Stripping - Waste Water Plant
- Ryan March
- Oct 17, 2023
- 5 min read
Phoenix Engineering designed and built the Methane Stripping Plant in 2020. The plant design was to reduce dissolved Methane in the leachate to below 0.14mg/l before discharge down an existing gravity pipeline. Air is bubbled through the leachate in a cascade four tank reactor sequence (half-life principle) to progressively reduce the dissolved Methane level. Testing after the plant was in operation proved the design to be working successfully and reducing the dissolved Methane to below 0.14mg/l consistently.
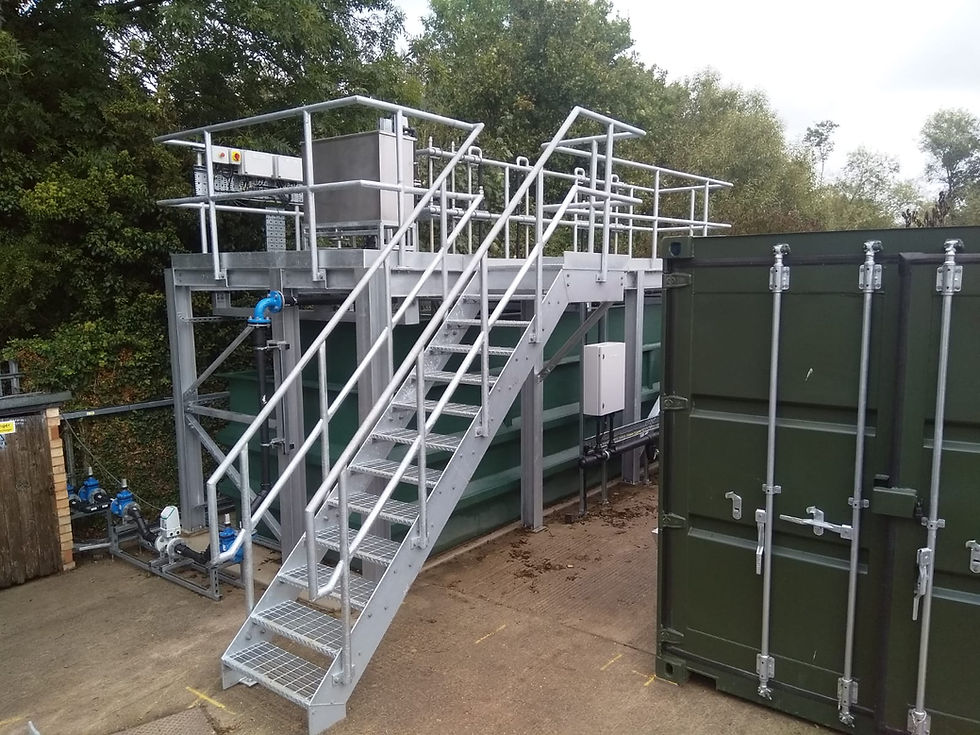
Scale: A hard deposit build up was observed after the plant had been running for some weeks which eventually resulted in restricting the discharge pipeline, coating the discharge pumps and reactor walls. After removal a sample was sent to ALS Laboratories for analyses and stated to be largely Calcium Carbonate.. Sequence of events On plants with light scaling a chemical additive is often used to remove or reduce the scaling. Phoenix conducted trials on dissolving the scale with chemical additives in their laboratory but concluded that the scaling at the plant was so severe as to render scale reduction by chemicals impractical and very costly.

COMPETITOR SYSTEM
Scale control by electronics - Scale control by using ionising of particles in the liquid is offered by many companies. After discussions and investigating the options, it was agreed to install the EM system on the pipeline at the plant. The MSP was drained and cleaned before the trial started. The EM Competitor system is a control panel with electronics attached to pads wrapped around the pipeline. The system remains on 24/7, Scale continued to build up after the system was set to work and after the trial period there was no reduction in the scale build-up, and it remained hard and difficult to remove.
Further searching found FlowScience had a similar system but with documented successful results when used on Leachate plants. It was agreed between the client Phoenix and FlowScience to install their system at the site on a trial basis to see if scale buildup could be reduced with their system. Phoenix removed the "Competitor" system and installed the FlowScience system when it arrived from Canada. The FlowScience system includes pads on pipelines (inflow and outflow), pads around discharge pumps and a free-standing pipe suspended in one reactor with pads.
First Trial The MSP was observed over the next months to determine what effect the FlowScience system had on the scale buildup. Whilst there were signs of less rapid buildup and that the scale was no longer a hard deposit it still resulted in the flow through the plant failing. Flow rates dropped throughout the trial period and discharge pumps had burnt out. It was felt the trials showed a partial success but had not controlled the problem of Calcium buildup inhibiting the plant. Discussions concluded that a second trial would be worthwhile with an additional pad unit on the final discharge point, an additional suspended pad unit in the third reactor tank and replacing the pumps with plastic units instead of the original stainless-steel pumps. It was felt that the stainless-steel pump jackets were inhibiting the pad pulses from entering the pump. 1.5. Second Trial Phoenix prepared a statement for the pump change and installation of the additional controls and a trial format that included regular observations and tests by Phoenix engineers. It was agreed that the trial should have an eight-week duration during which testing would be photographed for the records with some video as appropriate.
This second trial was managed to reduce the impact on other Phoenix commitments and therefore was agreed as a random attendance to site to work around these other commitments. Attendance dates therefore vary. RAMS and outline were submitted to the client along with the Phoenix “Buddy” system details for lone working. The client issued approval providing that the client were informed before each visit. This could be a simple phone call or email. At each visit the flow out was checked on the SCADA for consistency. This was also monitored remotely by Phoenix. Some inconsistency in the flow rate was noted but felt to be caused by the gravity discharge pipeline. Overall discharge flows remained constant throughout the trial. On each visit all pad functioning was checked with the Gauss meter to prove to be working. Photos are on the Phoenix server but not added to this report. To achieve testing of pads on the suspended pipe / pads they were lifted, scale visually checked, and a Gauss meter reading observed. The discharge pumps were also lifted on each visit to check the pads were functioning and observe the scale build up. The discharge header tank was checked on each visit and whilst some scale was visible it was minimal and soft. There was no sign of any scale build up in the discharge pipe mouth. On the final visit our engineer lowered the leachate level in the final reactor chamber to investigate scale build up on the walls. Some scale had formed 5 to 10mm thick. The engineer used a rod to scrap the scale which was soft and came away easily exposing the tank wall.
Pipeline inspection 8th September 2023 On 8th September the client had the discharge line inspected. The flow during the trials was constant but lower than expected. Inspection indicated that whilst there is some build up of soft scale flow was not inhibited by the scale. It is thought the main flow inhibiting was caused by a partial block from a harder substance, possibly some of the original scale that remained in the system and has worked loose. The photograph below shows the blockage at the joint before the bridge over the river. Other photographs show a build up of slimy scale which partially restricts flow and would indicate a periodic pressure washing of the discharge pipe may be required. Since removal of the blockage discharge flow rates have doubled. 2. Inspection after trial AT POINT A 9 2.2.
Before trial November 2022 For comparison these photographs show hard scale further downstream in the sewer from Nov 2022. There was no investigation in this section of the sewer after the trial, but it is felt that if similar conditions exist now then it would have been reported to the client. Reactor tanks after trial before cleaning 11th September The photographs below show soft scale on the walls of the reactors. Tank 1 Tank 2 Tank 3 Tank 4 Discharge Tank 3.3. Recommendations That the client consider accepting the system as a working solution to the operating problems at the plant.
SUMMARY & CONCLUSIONS
Shortly after start-up a very slight deposit can be seen on the pumps -21-06-2023. Two days later showed little change on the pumps. 2nd visit - no change 3rd visit - no change 4th visit - slightly more scale but reported as soft. 5th visit – no change 6th visit – no change 7th visit – no change 8th visit – no change on pumps. Discharge tank shows slight soft scale buildup and no restrictions to the discharge pipe. 9th visit – no change 10th visit – During this visit the reactor chamber level was lowered to observe the tank wall scale. A video was taken to show the deposit was thin and soft. Prior to the 10th visit one discharge pump had failed. Our engineer removed the volute, and it clearly shows there is no scale build-up. The likely cause is a capacitor failure not related to the trials.
CONCLUSION
The plant is running as per design with no signs of scale inhibiting performance. Some scale has appeared during the trial but is slight and soft and therefore not inhibiting the plant operation. Ongoing it is recommended that checks are undertaken, as in the trial, during the maintenance visits. Note ; Whilst the control panels are rated at 10amps each the running current is under 1 amp. Running costs are therefore minimal.
It is therefore considered the trial was a success and proved that the FlowScience system works at the plant and will enable the plant to operate without costly strip down cleaning cycles
For the Full Report DOWNLOAD HERE
Comments